Brauchen wir als Unternehmen Kennzahlen wie die OEE ?
Für Unternehmen, die TPM praktizieren wollen, ist das ein Muss, heißt es. Denn die Lean-Philosophie besagt, dass Verluste eliminiert werden müssen und OEE misst diese Verluste.
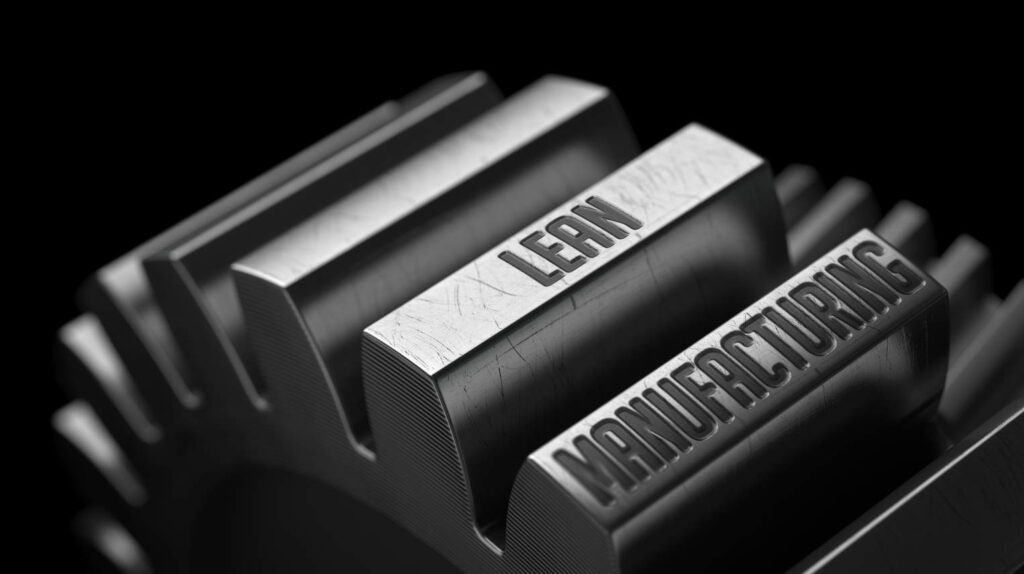
Wissenschaftlich betrachtet sind echte Lean-Unternehmen erfolgreicher als Unternehmen mit klassischer Kostenorientierung. Somit kann die Frage, ob OEE gebraucht wird, klar mit „Ja“ beantwortet werden.
Aber was ist nun so besonders an OEE und warum tun sich so viele Unternehmen schwer mit dieser Kennzahl?
Ich habe die Überschrift „Fluch und Segen“ genannt, weil es die zwei Seiten dieser Kennzahl gibt.
Fluch
Fangen wir mit dem „Fluch“ an.
Es gibt keinen einheitlichen Standard zur OEE. Die einen übersetzen OEE mit Overall Equipment Efficiency und die anderen mit Overall Equipment Effectiveness. Genau so variiert die Anzahl der in der Berechnungsformel verwendeten Verluste. Auch bei der Berechnung der Soll-Geschwindigkeit herrscht Uneinigkeit.
Die Führungskräfte hierzulande sind kulturell auf eine Kostenorientierung geprägt. Das bedeutet, sie arbeiten mit Kennzahlen, die (fast) immer ein €-Zeichen beinhalten. Der Euro stellt einen ganz klar definierten Wert dar. Jeder Mensch hierzulande wird täglich damit konfrontiert. Wir erhalten unser Gehalt in Euro und bezahlen in Euro.
Wenn ich also im Betrieb mit Kostenkennzahlen hantiere, kann das Gehirn das wunderbar verarbeiten. Das Ziel, Kosten einzusparen, erzeugt in unserem Gehirn ein klares Bild. Wenn wir zum Beispiel Personalkosten einsparen wollen, können wir genau berechnen, wie viel Mitarbeiter wir entlassen müssen, um das Ziel zu erreichen. Die Sache hat nur einen Haken. Wir können die langfristigen Auswirkungen nicht abschätzen, die wir mit solchen Maßnahmen auslösen. Im Vordergrund steht für viele Mitarbeiter erst einmal die Zielerreichung, an denen die meisten von ihren Vorgesetzten gemessen werden.
Langfristig betrachtet, kann eine Kosteneinsparung eine Kostenerhöhung bedeuten. Vielleicht hatte der entlassene Mitarbeiter über spezielles Know-how verfügt, dass jetzt fehlt und dadurch wird die Produktion des Produktes teurer.
Ganz anders sieht es bei der OEE aus. Sie stellt für uns keinen definierten Wert dar. Erschwerend kommt hinzu, dass die Berechnung relativ komplex ist: Verfügbarkeit x Leistung x Qualität. Ach herrje, was ist das denn ???
Nur Spezialisten, die sich tagtäglich damit auseinandersetzen, kennen die Formel auswendig. Dann hat der Wert an sich gar keine Aussagekraft. Wenn eine Maschine 50% OEE hat, kann das sehr schlecht sein, kann aber auch Weltklasseniveau bedeuten. Und jetzt kommt der Hammer – OEE enthält gar kein €-Zeichen. Da sagt uns unser Gehirn: „Das kann einfach nicht gut sein“. Aber das ist noch nicht alles. Im Gegensatz zu den Kosten, wissen wir meist gar nicht, wie wir diese Kennzahl beeinflussen können. Die Beeinflussung der OEE basiert häufig auf Vermutungen.
Beispiel: Wenn wir Kleingruppenaktivitäten zulassen und die Wartungszeiten erhöhen, werden wir vermutlich eine deutlich höhere Ausbringung erzielen. Die Kosten für Gruppen- und Wartungszeit kann ich berechnen, aber den Nutzen nicht. Somit sind das Dinge, die völlig undefiniert sind und bei denen ich das Kosten/Nutzen-Verhältnis nicht berechnen kann. Da schaltet jedes Gehirn sofort auf Alarmstufe rot. Mit undefinierten Zahlen und Vermutungen arbeiten, das ist ein Unding für jeden Firmenchef. Genau das Gegenteil fordert er doch tagtäglich ein.
Dann lieber auf Nummer sicher gehen und bei dem Bewährten bleiben. So sind wir Menschen programmiert.
Segen
Aber jetzt kommen wir mal zu dem Segen.
Wir würden nicht über OEE diskutieren, wenn es nicht diese sensationellen Erfolge geben würde, die Firmen damit erreicht haben und aktuell immer noch erreichen.
OEE hat nämlich einen ganz großen Vorteil:
Während eine direkte Kosteneinsparung, wie schon erwähnt, negative Auswirkungen haben kann, ist eine Steigerung des OEE-Wertes fast nie mit Nachteilen verbunden. Um OEE zu beeinflussen, müssen wir Verluste beseitigen. Und Verluste sind etwas, was wir definitiv im Unternehmen nicht brauchen. Da zur Arbeit an der OEE immer motivierte Mitarbeiter notwendig sind, ist es zusätzlich noch förderlich für eine positive Unternehmenskultur.
Die Vermutungen, die wir anstellen müssen, haben sich in der Vergangenheit fast ausnahmslos bewahrheitet. Somit ist das Risiko relativ gering.
Aber ein großer Nachteil bleibt:
Die Führungskräfte müssen lernen umzudenken, und dass kann manchmal sehr schmerzhaft sein.
Empfehlung aus der Praxis
Abschließend meine Empfehlung zu dem Thema:
Ich habe die besten Erfahrungen damit gemacht, die OEE als Effizienzkennzahl (Overall Equipment Efficiency) mit den sogenannten 7-Verlusten zu berechnen, wobei ich als Grundlage der Geschwindigkeitsverluste in der Regel die theoretisch maximal mögliche Geschwindigkeit der Anlage nehme.
Anlagenausfall
Rüsten und Nachstellen
Werkzeugwechsel
Anlaufverluste
Kurzstillstand und Leerfahrt
Geschwindigkeitsverluste
Ausschuss und Nacharbeit
Das hat folgenden Grund:
Erst einmal geht es darum, mit den jeweils vorhandenen Ressourcen einen höheren Output zu erzielen. Dazu kommt, dass eine Kennzahl nur Sinn macht, wenn ich sie beeinflussen kann. Diese 7-Verluste können alle vom Bedienpersonal bzw. einem Bedienerteam beeinflusst werden. Somit ist sie ideal als Zielwert für den Shopfloor geeignet.
Sobald ich andere Verluste, wie zum Beispiel Materialmangel, Personalmangel oder Wartungszeiten mitberechne, wird die Kennzahl für die Bedienerteams nicht mehr in allen Punkten beeinflussbar. Das führt erfahrungsgemäß immer wieder zu großen Problemen.
Natürlich sind diese Verluste auch von Bedeutung. Allerdings sind sie eher von Führungskräften und Management beeinflussbar.
Da die Hebelwirkung der Effizienz mit den sieben Verlusten erfahrungsgemäß am größten ist, lege ich gerade in den ersten Jahren einer Lean/TPM-Einführung immer den Fokus auf die Effizienz. Das entspricht auch der Lehre des JIPM (Erfinder des TPM).
Die anderen Verluste mit einzubauen und die Kennzahl dann als Zielwert zu nehmen, beinhaltet zu dem ein Risiko. Denn 10% mehr an Wartungszeit, können 40% mehr an Effizienz bedeuten. Aber rein rechnerisch (wir wollen ja immer alles berechnen), würde eine Verringerung der Wartungszeit erst einmal eine Verbesserung der Kennzahl bedeuten, was sich aber in der Folge selten bewahrheiten wird.
Ich würde eher dazu raten, diese Verlustwerte separat zu erfassen und zu bearbeiten.
Wenn wir einmal beim Beispiel Wartungszeit bleiben, so sollte ich daran arbeiten, die betroffenen Mitarbeiter zu trainieren und den Prozess der Wartung selbst, verlustfrei und somit effizienter zu gestalten.
Fazit
Mein Fazit: OEE sollte unbedingt als Zielkennzahl für den Shopfloor eingesetzt und als Gesamtanlageneffizienz betrachtet werden. Der Fokus auf diese Kennzahl wird den gewünschten Erfolg bringen.
Ihr Ulrich Schleuter