Die drei grundlegendsten Begriffe sind Opex, Lean und TPM. Das ist der Anfang. Der Beitrag wird diese Begriffe einführen und die Zusammenhänge vermitteln.
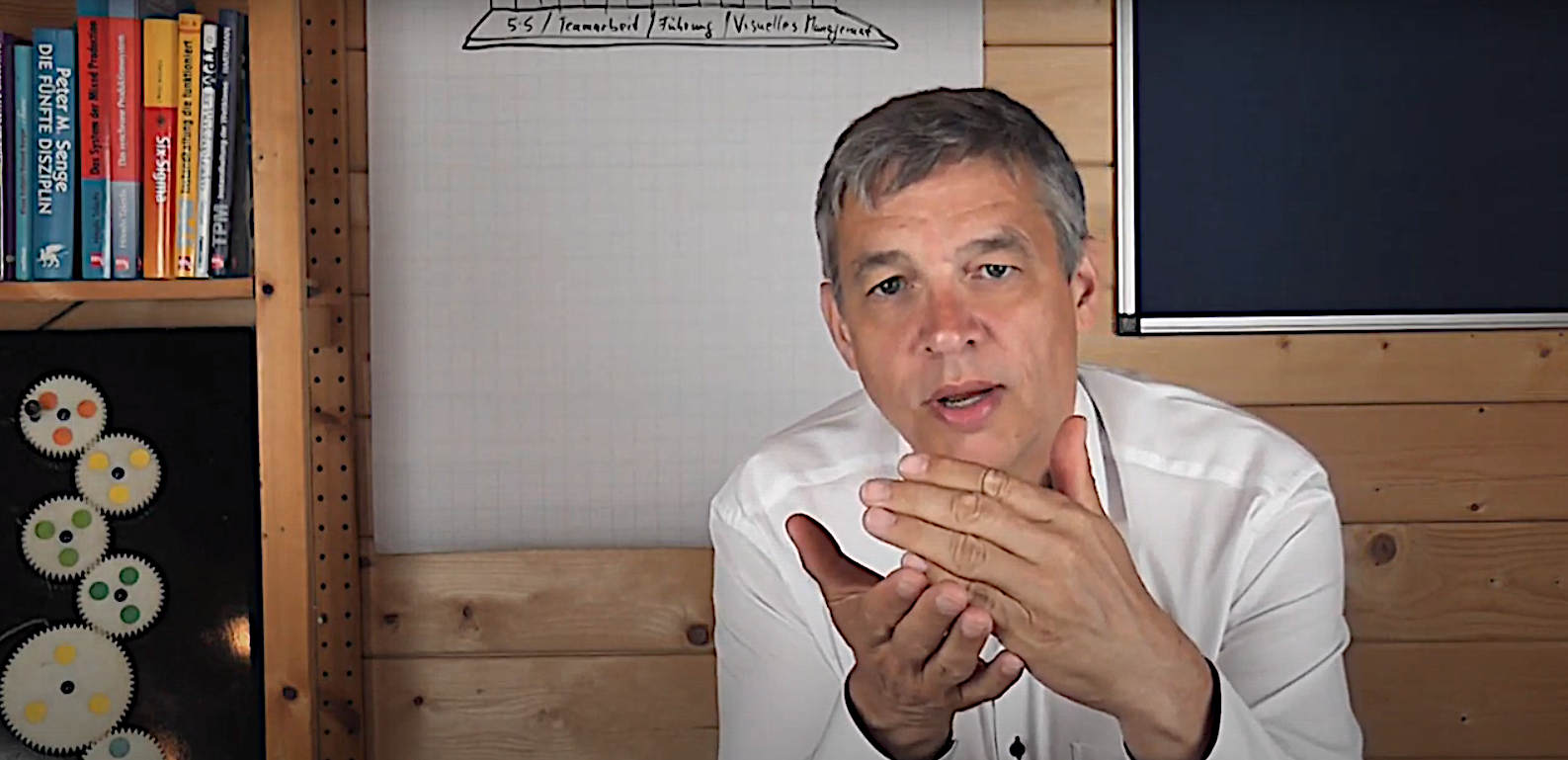
Worum geht es?
Im Folgenden werde ich meine Sichtweise der oben genannten Begriffe beschreiben, sowie auf Fakten der damit zusammenhängenden Themen eingehen. Opex, Lean und TPM sind eng miteinander verbunden. In welcher Art und Weise dies zutrifft, wird im Verlauf dieses Beitrags klarer.
1. Opex (Operational Excellence)
Etliche Experten haben in den letzten Jahren um Opex herum viele verschiedene Konzepte entwickelt. Für mich stellt Opex in erster Linie ein Zustand dar. Und zwar einen anzustrebenden Zustand. Ich sage meinen Kunden immer, unser Ziel muss es sein, den Zustand des Opex zu erreichen. Also einen exzellenten Zustand, mit dem man sich auf dem Markt von der Masse abhebt, also in der „Championsleague“ mitspielt.
2. Lean oder Lean Production
Am Anfang der 90er Jahre erschien ein Buch „Die zweite Revolution in der Automobilindustrie“ von James P. Womack. In diesem Buch wird die Philosophie, welche man bei Toyota verfolgt, hervorgehoben und als lean bezeichnet. Lean Production stammt jedoch nicht von Toyota, sondern vom Autorenteam um James P. Womack.
Lean bedeutet übersetzt „schlank“. Im übertragenen Sinne bedeutet lean jedoch, dass man sein Unternehmen auf eine besondere Art und Weise zum Erfolg führt, indem man alles, was nicht der Wertschöpfung dient, eliminiert.
2.1 Der verschwendungsfreie Zustand
Im Vordergrund steht hier der Aspekt der Verschwendung oder vielmehr die Anstrebung eines verschwendungsfreien Zustands in der Produktion. Um Verschwendung zu vermeiden, bedient man sich verschiedener Ansätze, wie z. B. Just-In-Time, der Nivellierung der Produktion, sowie der Möglichkeit der Implementierung einer Fehlererkennung in den Produktionsmaschinen.
2.2 Verschwendung erkennen
Jene Fehlererkennung kann in einem Fehlerfall Verluste und Verschwendung effektiv anzeigen und melden. Nicht zuletzt ist auch TPM ein Ansatz im Lean-Konzept, auf den ich im Folgenden noch näher eingehen werde. Allerdings kann die Technik einen verschwendungsfreien Zustand nicht selbst herbeiführen, sondern nur Menschen sind in der Lage, Verschwendung zu erkennen und zu eliminieren.
3. TPM (Total Productive Management)
TPM ist die älteste der genannten Begrifflichkeiten. TPM (Total Productive Management) ist ein Konzept, oder etwas präziser, ein ganzheitliches Managementkonzept. Ohne TPM hätte es z. B. das Produktionssystem von Toyota, wie wir es in der heutigen Form kennen, nicht gegeben. Ohne TPM hätte sich beispielsweise Just-In-Time bei Toyota nicht realisieren lassen können. Denn erst durch TPM lassen sich die Prozesse im Shopfloor stabil implementieren, welche es bedarf, um lean zu sein.
3.1 Instandhaltung
Betrachtet man die Prozesse im Shopfloor etwas näher, erkennt man recht schnell, dass die Thematik der Instandhaltung eine große Rolle spielt und jene Instandhaltung wurde somit zum Forschungsgegenstand. Eine japanische Forschungsgruppe nahm also ihre Arbeit in den Produktionswerken einer Toyota-Tochterfirma namens Nippondenso auf. Diese Forschungsgruppe hatte den Namen JIPE (Japan Institute of Plant Engineering) und wurde von Seiichi Nakajima geleitet.
3.2 Der Mensch im Mittelpunkt
Ende der 60er Jahre erzielte man dann bei Nippondenso einen Durchbruch während den Forschungsarbeiten und man erkannte, dass für die Instandhaltungsaufgaben das Bedienpersonal der Maschinen einfach ausschlaggebend und unumgänglich ist. So wurde sehr klar, dass der Mensch, hier als Bedienpersonal, unbedingt im Mittelpunkt stehen muss. Durch diese Sichtweise erreichte man extrem hohe Effizienzwerte in der Produktion. Das heute bekannte TPM wurde somit geboren. Heute ist TPM nach wie vor als Instandhaltungskonzept ein ganz wichtiger Bestandteil des Toyota-Produktionssystems. Später wurde JIPE umbenannt in JIPM (Japan Institute of Plant Maintenance) und es wurde weiter an TPM geforscht, so dass TPM heute ein ganzheitliches Konzept geworden ist.
3.3 Die acht Säulen des TPM
Bei Nippondenso waren es im ersten Ansatz lediglich vier grundlegende Kriterien, welche man erkannte. Die einzelnen Kriterien des TPM werden in der Literatur auch gerne als Säulen bezeichnet, so dass im ersten Anlauf die folgenden ersten vier Säulen definiert wurden:
- die autonome Instandhaltung
- die geplante Instandhaltung
- Schulung und Training des Personals (immer fortwährendes Training)
- Kaizen (kontinuierliche Verbesserung – hier angewendet, um Verschwendung stetig zu eliminieren)
Nachdem jedoch diese vier Säulen aufgestellt wurden, erkannte man weiter, dass noch mehr dazu gehört bzw. noch mehr Potenzial in der Gesamtthematik schlummert. Man forschte also weiter und es wurden nochmal vier weitere Säulen aufgestellt:
- das Maschinenanlaufmanagement
- die instandhaltungsfokussierte Qualitätssicherung (Quality Maintenance)
- die Sicherheit, der Umweltschutz und die Gesundheit
- TPM in indirekten Bereichen (also nicht nur in den wertschöpfenden Bereichen)
3.4 Flexibilität
So entstand ein ganzheitliches Konzept, welches dermaßen flexibel ist, dass es sich in jedem beliebigen Unternehmen implementieren lässt. Die Flexibilität des Konzepts war immer großer Forschungsgegenstand, den man von vorne herein konsequent verfolgte. Es gibt sukzessive Vorgehensweisen um TPM einzuführen. Aus meiner heutigen Sicht ist TPM das Werkzeug, mit dem man lean wird.
3.5 Psychologie
Während der Einführung von TPM ist jedoch der Mensch immer wieder eine Herausforderung. Beim Thema Unternehmenserfolg stehen wir uns zumeist selbst im Weg. Da TPM nun in Japan entwickelt wurde, sah man sich anfänglich natürlich nur mit der japanischen Mentalität konfrontiert, vor dessen Hintergrund TPM entwickelt wurde. Japanische Unternehmen sind streng hierarchisch aufgebaut und die Mitarbeiter (das Bedienpersonal) schauen zu ihren Vorgesetzten als Untergebene hoch. Wenn in Japan ein Vorgesetzter etwas anordnet, dann wird dieser Anordnung unbedingt Folge geleistet. Hier in Europa herrscht aber eine andere Mentalität vor, so dass die psychologische Komponente ungleich größer ist als dies in Japan der Fall wäre. Der Mensch ist ein Gewohnheitstier, er möchte seine Gewohnheiten beibehalten und schaut daher in aller Regel der Einführung von TPM zuerst einmal eher skeptisch entgegen. Man muss überzeugen, um TPM konsequent einführen zu können und das Personal von Anfang an mit teilhaben lassen und aktiv einbinden.
3.6 Potenzial
Hier in Deutschland gibt es ein riesiges Potenzial für TPM, welches als Nachholbedarf zu verstehen ist, da es sehr viele Unternehmen gibt, welche die Vorzüge von TPM für sich noch nicht erkannt haben. Das ist tragisch, denn meine Erfahrungswerte bestätigen, dass sich ein konsequent eingeführtes TPM in jedem Fall auszahlt.